Sunday, 19 October 2014
Finishing off some old jobs
I am starting to run out of jobs! Strange feeling. The cabin lining will have to wait until next summer as I need warm dry weather to cut out the anchor locker hatch and glass over it. Recent small jobs were: finishing plumbing in the hatch drains (involved removing batteries and much wriggling in small spaces); smartening the cabin step, finishing lining the heads (loo) and installing a bilge monitor system. This warns if the bilge pump is running and also to warn if the pump has run while the boat was unattended. If you want to make one yourself, I have put full instructions here: http://www.boat-angling.co.uk/Hints_and_Tips/bilgemonitor.htm It looks like this.
Sunday, 21 September 2014
Fishing - or I could call it testing
Last weekend I managed to get half the hatch drain plumbed in, but I will have to remove the batteries to get at the other side and involves removing an unnecessarily large battery retainer just to get them out. This weekend's weather was too good to miss so that job can wait. I took Rebel Runner out fishing and here is proof that there is fish slime on that deck:
Some observations on recent additions: the new through-hull transducer was excellent, it held a strong bottom signal at all speeds. Or it did after I realised I had set it to a max depth of 10 feet and forgot to reset it to Auto, resulting in a long period of blank screen. The Garmin 551 Downvu works well, although the Flag Theofano wreck is still a lump. I will have to find something more interesting to look at. Finally, the outdrive leg trim sensor is now all wired up so I played with the trim. Unlike my previous deep vee hull, the higher the trim the worse the performance. Trimmed to midway, it wouldn't go faster than 13.6 knots. Trimmed nose down it immediately flew to 20 knots which is dramatic. I have been looking at Bennet trim tabs to help adjust the list to port at full throttle. They may also help fine-tune the bow attitude. I think I will fit those next lift-out.
Sunday, 14 September 2014
Night job...
And the job I couldn't do earlier - the extra long skin fitting turned up from ASAP Supplies dead on time. I had to buy a costly bronze one but it was a perfect fit. Launch was booked for Friday so my only window was Thursday night. It took three goes to get the hole cutter through 65mm of transom but it went through, then a lot of grunting and wriggling to get the securing nut done up, as it was behind the engine and exhaust. After that it was a simple matter to screw on the scupper fitting over it. I had made a spacer to clear the skin fitting by cutting up a chopping board. My wife keeps wondering where the boards are going. I fitted the hose on the inside and looped it up to keep the water out until I can get under the hatch to connect the other end. All this with a head torch as the work lamp was blinding me!
![[IMG]](http://i245.photobucket.com/albums/gg52/flying-ferrets/scupper.jpg)
Sunday, 7 September 2014
Annual antifouling lift-out (already???)
It's been a year! About this time last year Rebel Runner came over from Cowes in her "raw" state, for an engine service, survey and antifouling. A year later she needs antifouling again so she has been lifted for the annual work. This was the weekend of hard graft, trying to cram in all the jobs that can only be done out of the water. Firstly, antifouling. I thought that would be simple but I noticed the scum lines on each side were different. Worrying about a list, I measured them and found the port waterline a good two inches lower amidships. That meant I had to measure up, mark, rub, prime and only then start antifouling again. As a ruler I used a length of plastic conduit as the cheapest long straight bendy thing in B&Q (79p). In between coats of boot topping I installed the transducer for the Garmin 551dv:
Problem #1: Unfortunately the cable was too short so I have to order an extension. At least that won't stop anything else.
Next job was to install the Airmar through-hull transducer. This involved drilling a 60mm hole (scary) and a tile drill was perfect. Problem #2: the transducer nut is three inches across and nothing I had was big enough, and nothing in B&Q either. Problem solved the following morning by using a G-clamp as a spanner.
Then a polish, I used Farecla Hull Restorer which includes a wax. Shiny or what?
The next job was the fit the transom drain outlet for Garry's hatch. Problem #3: the transom is 65mm thick!!! My skin fitting was standard (30mm) so a quick order to ASAP Supplies for a longer one is required. Fingers crossed they do their usual amazing service and I'll receive it in time for an evening job.
Final job was a filler really, I installed a mount for my iPad. I had spent a long time wondering where to put it, and this is the result. I cut part of the mount off and screwed it through the wheelhouse front. There is a dome nut outside but you can barely see it.
Just as I was clearing up on Sunday evening there was a knock on the hull and a tired looking Steve was there with a gift of two bass! What a nice pontoon neighbour. He had been fishing since Friday hence the look, hauling bass for three days can do that to a man. Let's hope everything comes together by Friday so I can get out to them too. Thanks again Steve!
Problem #1: Unfortunately the cable was too short so I have to order an extension. At least that won't stop anything else.
Next job was to install the Airmar through-hull transducer. This involved drilling a 60mm hole (scary) and a tile drill was perfect. Problem #2: the transducer nut is three inches across and nothing I had was big enough, and nothing in B&Q either. Problem solved the following morning by using a G-clamp as a spanner.
Then a polish, I used Farecla Hull Restorer which includes a wax. Shiny or what?
The next job was the fit the transom drain outlet for Garry's hatch. Problem #3: the transom is 65mm thick!!! My skin fitting was standard (30mm) so a quick order to ASAP Supplies for a longer one is required. Fingers crossed they do their usual amazing service and I'll receive it in time for an evening job.
Final job was a filler really, I installed a mount for my iPad. I had spent a long time wondering where to put it, and this is the result. I cut part of the mount off and screwed it through the wheelhouse front. There is a dome nut outside but you can barely see it.
The iPad mount clamps on the cog and is still fully adjustable.
Just as I was clearing up on Sunday evening there was a knock on the hull and a tired looking Steve was there with a gift of two bass! What a nice pontoon neighbour. He had been fishing since Friday hence the look, hauling bass for three days can do that to a man. Let's hope everything comes together by Friday so I can get out to them too. Thanks again Steve!
Sunday, 31 August 2014
More progress and a bonus
A successful day on several fronts. One unexpected bonus was that I got my trim gauge working. I had given up thinking the sender was kaput but I was doing a tidy of wires before I boxed in the panel behind the dash and I noticed...a stray power wire. Gauges do not work without power. I have no idea why I hadn't connected that but now it is connected and now the gauge works. So simple. This is what the wiring looked like before....
Finally I fitted some neat clips to hold the fenders on the rails. When I have to tie on or untie six fenders on my own before coming up the channel I can be swept a couple of hundred yards in the Langstone Run, clipping these on should make that job a doddle.
When I was looking for photos of Garry's galley in its finished condition I realised I hadn't any. Here are a couple of shots. I am really pleased with it.
Finally I fitted some neat clips to hold the fenders on the rails. When I have to tie on or untie six fenders on my own before coming up the channel I can be swept a couple of hundred yards in the Langstone Run, clipping these on should make that job a doddle.
When I was looking for photos of Garry's galley in its finished condition I realised I hadn't any. Here are a couple of shots. I am really pleased with it.
Monday, 25 August 2014
How not to test a loo
Been quiet for a bit, family visits and all that but I have been doing a few jobs, including painting the heads with Jotun Hardtop two pack in white. I'll add a fiddle rail in teak rather than box in that useful shelf. I also plan to put a curtain over the door rather than a hard door as it is very cramped in there.
It went a bit quiet and an hour later something needed to be done Time to test the loo! What could possibly go wrong? Water pumped in fine. Did the deed. One pump. Fine. Two pump. Fine. Three pump. Resistance! Hard pump. And with that a 360 degree Catherine wheel of you know what came out of the back of the pump arrangement. I was then faced with a loo bowl full of brown otters and a speckled effect white Jotun loo cubicle. Nothing for it but to get bucket, rubber glover and bleach spray and get to work. Not great as by now it was blowing a beam F3. After all was cleaned up I left it until I got back to the marina before investigating further. Meanwhile I had caught another bass on BBQ pout! Result. When I finally got back in the berth, all I needed to do was tighten up all the screws on the pump and it pumped through fine. I may test it with something else, not poo, next though.
I tested the loo by pumping water in and pumping water out. All fine. On Sunday I decided to go fishing rather than spend the day fitting things so I headed out to find mackerel. No joy at all so rather than waste time I went straight to my mark and used frozen squid. Pretty soon I had a few small pouting so one went back down again barbecue-style. This is the result. First serious guts on the deck! 7lb 8oz
It went a bit quiet and an hour later something needed to be done Time to test the loo! What could possibly go wrong? Water pumped in fine. Did the deed. One pump. Fine. Two pump. Fine. Three pump. Resistance! Hard pump. And with that a 360 degree Catherine wheel of you know what came out of the back of the pump arrangement. I was then faced with a loo bowl full of brown otters and a speckled effect white Jotun loo cubicle. Nothing for it but to get bucket, rubber glover and bleach spray and get to work. Not great as by now it was blowing a beam F3. After all was cleaned up I left it until I got back to the marina before investigating further. Meanwhile I had caught another bass on BBQ pout! Result. When I finally got back in the berth, all I needed to do was tighten up all the screws on the pump and it pumped through fine. I may test it with something else, not poo, next though.
Wednesday, 6 August 2014
Various jobs and a short cruise
After a gap in reports due to a holiday, I spent a morning on Rebel Runner before taking her out on a little trip in the afternoon. I had been in California and among other toys I brought back a lure and trace holder, which I cut in two and fitted each side of the wheelhouse "wings". In fact, having reflected on how simple this is, it could easily be made from right angled plastic strip (less than £2 from B&Q) with small holes drilled in the sticking-out part and the flat glued to the boat with Sikaflex.
The next job wasn't so easy. The hatch in the cockpit is a heavy beast and if it fell shut it could be dangerous. I bought a heavy-duty spring to hold it up but unfortunately there is nothing to bolt it to at the side of the hatch as the gutter forms the rim. I made up a block of wood and intended to glass it under the gutter. Have you ever tried glassing upside down underneath yourself, where you can't see the back of it? Worse, every time I put a layer of mat on it slumped down. Eventually I decided to do it in stages, here are two layers on, another to go then a flow coat. Who would have thought such a small thing was so tricky.
Next job was a simple one - I had applied for a Small Ships Register number and it arrived a while back. It has to be displayed in 30mm text on each side, so I ordered vinyl lettering from The Sign Man (who supplied the boat name lettering) . I applied them to the stern quarter.
The next job wasn't so easy. The hatch in the cockpit is a heavy beast and if it fell shut it could be dangerous. I bought a heavy-duty spring to hold it up but unfortunately there is nothing to bolt it to at the side of the hatch as the gutter forms the rim. I made up a block of wood and intended to glass it under the gutter. Have you ever tried glassing upside down underneath yourself, where you can't see the back of it? Worse, every time I put a layer of mat on it slumped down. Eventually I decided to do it in stages, here are two layers on, another to go then a flow coat. Who would have thought such a small thing was so tricky.
At 2pm the marina gate opened but it was blowing a good F5 and all the charter boats were tucked up in their berths. Fishing seemed unlikely. We have family arriving from the USA soon and I am required to transport some of them to Bembridge for a family meet-up, so I thought I had better do a trial run as I haven't been to Bembridge harbour for a while. Rebel Runner behaved perfectly heading into a very short sea and 20 knot winds, feeling very steady and surprisingly dry, most of the spray was deflected well astern. As you could have guessed, Bembridge on a Sunday in Cowes week was packed, it felt like the M25 going in. Once I found the visitor's berths I turned round, job done, only to find a 30 foot yacht reversing at 90 degrees across the channel which is about 30 feet 6 inches wide. I have no idea what was going on, I just found a gap and went through. I had heard mackerel were appearing at The Forts so I headed over. First drop, a mackerel, then nothing for the next several drifts but it was very uncomfortable in the wind. At least I could claim fish guts on that flashy deck at last! Back to the marina for a through clean down, now she's all ready for visitors.
Sunday, 29 June 2014
Rebel Runner is a Ship, and a quieter one too.
A couple of things to report. Firstly, Rebel Runner is officially a ship! The certificate from the Register of British Ships Part III arrived today, not much - just a laminated A6 card - but she has a number and I will have to get it made up to stick on the side.
The other bit of progress was completing the new gutter on the old engine casing. The previous one was placed under the hinge crack to prevent water dripping onto the engine which worked fine until you opened the lid, when all the water ran onto the engine because the gutter was not wide enough. I cut the old one off and found it was just a piece of poly pipe laminated over. With much advice from Garry I used an old bed slat as a mould and laminated three layers of mat onto it. After it cured I popped it out, trimmed it up and bonded it in place with paste. I then put another three layers on. Trimmed again, filled various gaps and flo coated over. I also filled surplus screw holes and gel coat chips while I was about it. Sounds very cool and easy? No so. Garry will know, he had loads of texts and questions including when the parcel tape used to release the mould went all wrinkly and the result was a mess which needed much filling and sanding. Garry would have done it in minutes, I took half a day plus several evenings but here is the result.
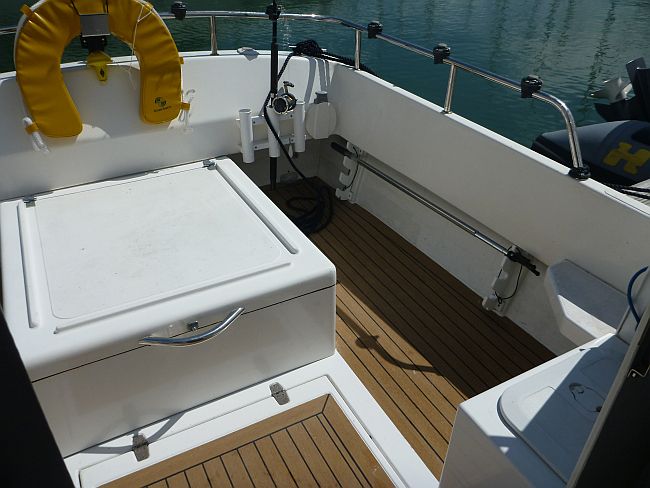
Next job was to fit the soundproofing mat I had bought on a special offer way back. One and a half sheets did the lid, and the three sides consumed most of two more. I finished the edges off with metal tape. You are supposed to use it for joining two sheets but I had plenty and it finished it off rather well.
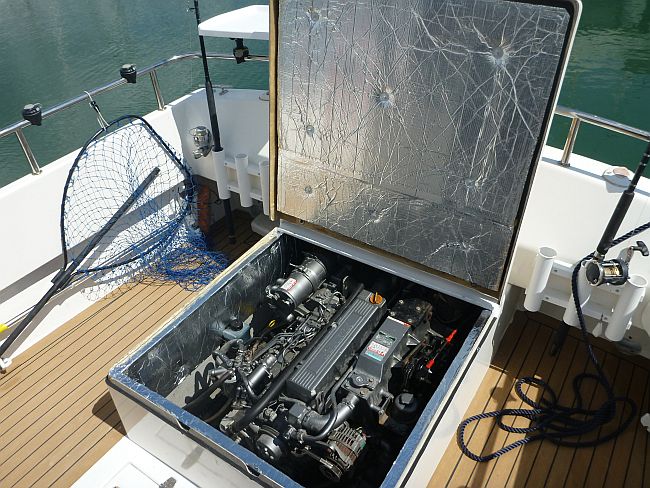
The engine started first turn as usual, it is still a growler but what do you expect for 260HP. I have done all I could. I took Rebel Runner out for a quick spin round the harbour entrance but no mackerel were evident so still no fish guts on that deck I'm afraid. Final job was to rub down and polish some gel coat patches on the roof then she was all tucked up ready for next time.
P.S.
This is what it looked like when I bought it.
The other bit of progress was completing the new gutter on the old engine casing. The previous one was placed under the hinge crack to prevent water dripping onto the engine which worked fine until you opened the lid, when all the water ran onto the engine because the gutter was not wide enough. I cut the old one off and found it was just a piece of poly pipe laminated over. With much advice from Garry I used an old bed slat as a mould and laminated three layers of mat onto it. After it cured I popped it out, trimmed it up and bonded it in place with paste. I then put another three layers on. Trimmed again, filled various gaps and flo coated over. I also filled surplus screw holes and gel coat chips while I was about it. Sounds very cool and easy? No so. Garry will know, he had loads of texts and questions including when the parcel tape used to release the mould went all wrinkly and the result was a mess which needed much filling and sanding. Garry would have done it in minutes, I took half a day plus several evenings but here is the result.
I took the engine casing back to the boat on Sunday, and trial fitted. As suspected, the extra layers of mat did make it jam when I tried to slot it in but a bit of grinding out fixed it. All polished:
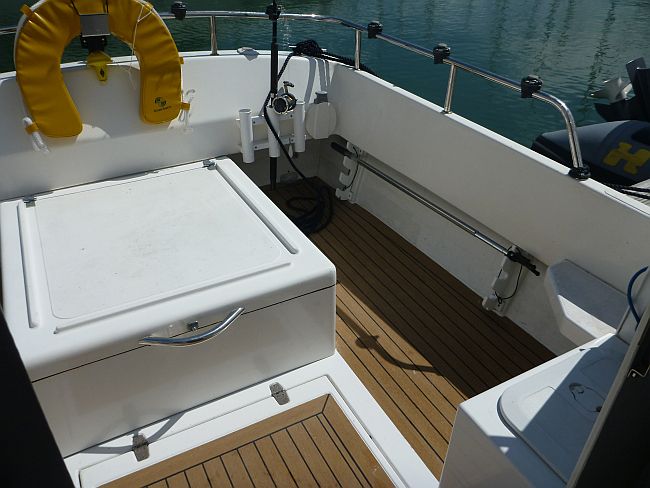
Next job was to fit the soundproofing mat I had bought on a special offer way back. One and a half sheets did the lid, and the three sides consumed most of two more. I finished the edges off with metal tape. You are supposed to use it for joining two sheets but I had plenty and it finished it off rather well.
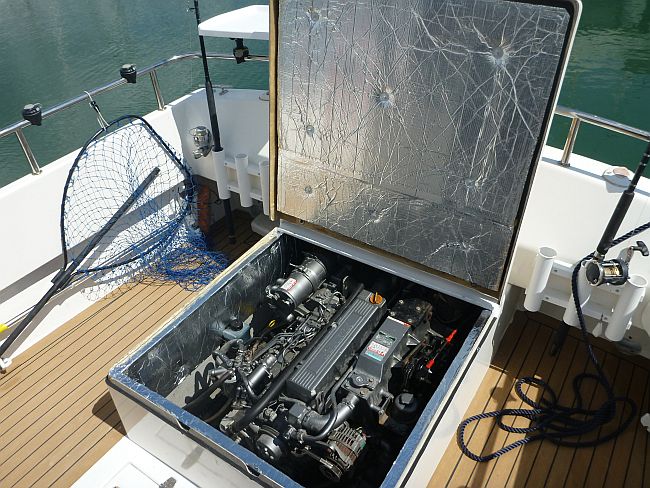
The engine started first turn as usual, it is still a growler but what do you expect for 260HP. I have done all I could. I took Rebel Runner out for a quick spin round the harbour entrance but no mackerel were evident so still no fish guts on that deck I'm afraid. Final job was to rub down and polish some gel coat patches on the roof then she was all tucked up ready for next time.
P.S.
This is what it looked like when I bought it.
Monday, 23 June 2014
New decking in the cockpit
Saturday -today's job was to fit the Permateek deck (if only to stop Garry nagging me about it!) Actually I'm just as keen to see it finished as he is. I started off with a visit to Garry to collect the empty drums he promised, to use as weights. He also cut me some mat to use to make new gutter in the engine box. Then off to the marina via BaseLine Marine to buy two catches for the electronics hatch (another job in progress). I eventually arrived at the marina, where it was dead calm and baking hot. Calm good, baking hot - not so good if the glue goes off! Anyway, on to work.
First take off the engine casing and wrap the engine up. Then sand down the deck, take off any lumps and bumps, and screw down an access plate that I am going to cover up. I measured carefully and recorded it in the back of the Log Book so I know where it is if I ever have to cut a hole. Then I had to do a thorough clean, and make any slight adjustments to the Permateek mats to make sure they fitted like a glove. There would be no second chances. The glue was in sausages so I had to invest in a sausage gun, expensive but worth it. After all that, each panel took about half an hour to fit, what with the gluing, spreading, fitting and rolling out. I weighted them down with wooden boards, Garry's drums and more buckets. The boat looked like it was about to make a drought relief trip up some African river. I took the engine casing home and tomorrow I'll make a start on the GRP work before going back tomorrow afternoon to see what the new deck looks like.
First take off the engine casing and wrap the engine up. Then sand down the deck, take off any lumps and bumps, and screw down an access plate that I am going to cover up. I measured carefully and recorded it in the back of the Log Book so I know where it is if I ever have to cut a hole. Then I had to do a thorough clean, and make any slight adjustments to the Permateek mats to make sure they fitted like a glove. There would be no second chances. The glue was in sausages so I had to invest in a sausage gun, expensive but worth it. After all that, each panel took about half an hour to fit, what with the gluing, spreading, fitting and rolling out. I weighted them down with wooden boards, Garry's drums and more buckets. The boat looked like it was about to make a drought relief trip up some African river. I took the engine casing home and tomorrow I'll make a start on the GRP work before going back tomorrow afternoon to see what the new deck looks like.
Sunday -part 2 of the decking installation. I spent the afternoon glassing up a new gutter in the engine casing, with real-time virtual help from Garry with text messages. I'll show photos when I have tidied it up, but it looks pretty good for a beginner. This evening I went back to the marina to see how the deck had stuck down. All the planks and Garry's drums seem to have worked. I emptied everything out, then spent ages masking all around the edges of each panel to caulk the gaps and ensure any water drains to the scuppers and doesn't settle and go green. The engine casing is still at home but here are a few shots of the new deck. Looks good.
Tuesday, 17 June 2014
Father's Day Photo-shoot
Father's Day today, so we made it a family occasion on Rebel Runner with a lunch on board. First however, I persuaded daughter Aedy and wife Olwyn to take a walk to the pier at the entrance to Langstone Harbour so Aedy could take some photos of Rebel Runner showing her paces. She did a great job with her pro camera, a selection reproduced here. Then we had a very pleasant lunch (a table! Seating!! Sink and Cooker!!!) So civilized. After lunch I went and collected a very important package from the marina office, but here are the action shots first:
That very important parcel was my Permateek decking and I must say Mike has done a brilliant job. Here is the hatch section just laid down for a preview
The side sections are all rolled up, I can't lay them until the engine casing is trimmed
A couple more:
Sunday, 8 June 2014
More things working now...
I only had a morning in the marina this weekend so I had to make it count. The weather was stunning, although probably a tad breezy further out (or so I told myself). First job was to make the fuel gauge work. I had ordered a new sender from A.s.a.p Supplies which arrived within a day as usual. I wired it up and slid the slidey thing up and down. The needle waved back at me so that looks alright. It was then a simple matter of undoing five screws, lifting the old sender out, dropping the new sender in, aligning the holes (note to others - for some reason the holes are not equally spaced so don't start screwing until you know holes and gasket are aligned) and tightening up. Re-do all the connections and we are back in business with a working gauge.
Next job was a bit more daunting and another one I had been procrastinating - drilling out the old sink drain to take the Webasto heater exhaust skin fitting. It was on the water side of the boat, not the pontoon but luckily there was nobody in the berth next to me so with a series of long warps and running back and forth I moved Rebel Runner about three metres right and tied up again.
The final job was to put the fuse back in, turn the heater control to Full, and see what happened. These days, machines can sort them selves out so after what seemed like minutes of glugging, whirring and blowing, she very quietly throbbed into life and blew nice hot air around the cabin. I won't be needing it just yet but it is a relief to know it all works.
Next job was a bit more daunting and another one I had been procrastinating - drilling out the old sink drain to take the Webasto heater exhaust skin fitting. It was on the water side of the boat, not the pontoon but luckily there was nobody in the berth next to me so with a series of long warps and running back and forth I moved Rebel Runner about three metres right and tied up again.
I had to be very careful about getting in and out, it would have been so easy to leap onto the port side to get out as I usually do, except that would have resulted in a bath.
The old skin fitting came off very easily, no problems there. Now I had to drill a 40mm hole on the same place, at an acute angle to match the angle of the pipe inside the skin fitting. There was no room inside so I have to hang over the side of the pontoon and drill up into the hull with a 240volt device in my hands inches above the water. Luckily the Elf and Safety Department was still tucked up in bed. All went well however, then I had to align the fitting in the hole while I drilled for the mounting screws.
I still have a vivid memory of sitting on the roof while an expensive 316 bolt went bounce bounce bounce plunk into the water. If I slipped, this skin fitting wasn't even going to do the bounce bit, just a straight plunk. I set up a contraption of cord so it could run up and down without falling in, which meant all I had to worry about was dropping drill, chuck key, mastic, screws, screwdriver and power cable. With dextrous fiddling and use of masking tape to hold things in place, one by one the screws were installed and tightened up. It would have been a lot easier with another pair of hands, but where's the challenge in that?
The old skin fitting came off very easily, no problems there. Now I had to drill a 40mm hole on the same place, at an acute angle to match the angle of the pipe inside the skin fitting. There was no room inside so I have to hang over the side of the pontoon and drill up into the hull with a 240volt device in my hands inches above the water. Luckily the Elf and Safety Department was still tucked up in bed. All went well however, then I had to align the fitting in the hole while I drilled for the mounting screws.
I still have a vivid memory of sitting on the roof while an expensive 316 bolt went bounce bounce bounce plunk into the water. If I slipped, this skin fitting wasn't even going to do the bounce bit, just a straight plunk. I set up a contraption of cord so it could run up and down without falling in, which meant all I had to worry about was dropping drill, chuck key, mastic, screws, screwdriver and power cable. With dextrous fiddling and use of masking tape to hold things in place, one by one the screws were installed and tightened up. It would have been a lot easier with another pair of hands, but where's the challenge in that?
The exhaust pipe was trimmed, lagged and clamped up to the skin fitting and we were nearly ready. Last job was to get fresh air from outside. The space under the side decks ends at the bulkhead, and the other side of the bulkhead is an open rope locker so that was the ideal place to put a vent and duct connector. When they design factory boats I bet they think these things through first. That 80mm hole would have taken moments to do while the bulkhead was lying on a bench, instead it was now in a place where virtually no power tools could reach. With a bit of this and a bit of that and at least half an hour of grunting I managed to carve a not very neat hole but as it is under the vent face nobody will see.
The final job was to put the fuse back in, turn the heater control to Full, and see what happened. These days, machines can sort them selves out so after what seemed like minutes of glugging, whirring and blowing, she very quietly throbbed into life and blew nice hot air around the cabin. I won't be needing it just yet but it is a relief to know it all works.
Thursday, 5 June 2014
Fitting and Fishing
This Saturday promised to be sunny and settled. Time for a bit of fishing, although I had a few jobs to do first. The management decided she wanted a new Turtlemat doormat for the house. I sneaked an order in for a marine one at the same time. Wipe your feet!
I have long promised new decking in the cockpit, but it has taken a while to happen. I phoned the Permateek man who was supposed to be taking the template and found he was running behind, work-wise (what's new?). He kindly sent me a pack of templating material so I could mark up the deck area and move things along a bit. With Mike's instructions this was surprisingly easy, I guess it wouldn't have been if has been in any way wet or windy! The material was as see-through as tracing paper but strong, more like a man-made fabric. Hopefully the panels can now be made up and I'll have a go at fitting.
Next job was investigating why the fuel tank sender wasn't working. I measured up for a new one, as it is a sealed unit and there is nothing that can be repaired.
Another quick repair job, to replace the shore-power socket and then the marina traffic lights went green and we could go to sea. I headed out after that, hoping for bream. Rebel Runner cruised easily at 20 knots and took me to Bullocks Patch. One thing I hadn't shown before - I designed the mast to have a halliard point for a pennant or anchor ball. Worked well.
I have long promised new decking in the cockpit, but it has taken a while to happen. I phoned the Permateek man who was supposed to be taking the template and found he was running behind, work-wise (what's new?). He kindly sent me a pack of templating material so I could mark up the deck area and move things along a bit. With Mike's instructions this was surprisingly easy, I guess it wouldn't have been if has been in any way wet or windy! The material was as see-through as tracing paper but strong, more like a man-made fabric. Hopefully the panels can now be made up and I'll have a go at fitting.
Next job was investigating why the fuel tank sender wasn't working. I measured up for a new one, as it is a sealed unit and there is nothing that can be repaired.
Another quick repair job, to replace the shore-power socket and then the marina traffic lights went green and we could go to sea. I headed out after that, hoping for bream. Rebel Runner cruised easily at 20 knots and took me to Bullocks Patch. One thing I hadn't shown before - I designed the mast to have a halliard point for a pennant or anchor ball. Worked well.
The Harley 25 has a very stable hull at anchor, much better than the Trophy on a beam wind as we had on Saturday. Actually it was very comfortable, great for having a brew in the galley, and washing up after too! After a pollack, some nice smoothhound and numerous pouting, it looked like the bream weren't playing so I headed back to Hayling Bay. First drop, a bream. second drop, a smoothhound, then nothing so I headed in just before the gate closed. I still haven't got used to the handling so I made another mess of getting into the finger berth, but not as badly as before so at least there is some improvement

Monday, 26 May 2014
More work, more progress.
Another weekend, another day of graft. The weather wasn't kind on Monday so I spent most of the time inside while the rain drummed on the roof. Nice and cosy now though. First job was to fit the footrest, an inspired idea from this forum. Folded away neatly:
Then I stuck my head under the crew seat and finished off all the wiring and venting for the Webasto heater. There are only two tasks left: fitting the exhaust skin fitting and the fresh air intake. Both outside jobs, and driving rain is not required.
And deployed for use:
Then I stuck my head under the crew seat and finished off all the wiring and venting for the Webasto heater. There are only two tasks left: fitting the exhaust skin fitting and the fresh air intake. Both outside jobs, and driving rain is not required.
When the boat arrived it had a Navico multi function display with through hull transponder, speed, temperature and timing features. It was removed to make way for the Garmin set-up. I decided why waste it, it has useful features and could always be a back-up. I took the cup-holder off and installed it in its place. That should have been simple, but behind that bulkhead was the black box sounder which had to be moved, and I had run out of fuse spaces. So I had to put in a new fuse block and another ground bus-bar, but that would come in useful later.
My Icom handheld VHF came with a charging base, and it makes a secure holding-place. I screwed it to the side shelf and routed the charging cable back to the electrics behind the bulkhead, making a permanent fixture.
And then...the rain eased off! Time for a quick outside job before home. I had bought two sets of rod holders which were fitted at the stern. Did I mention I love this work so much I do it twice? First time round the rod holders were fitted upside down. Lucky I noticed before looking at the photo! You can also see the life belt and holder fitted previously.
The next major job will be lining out the cabin. Watch this space

Subscribe to:
Posts (Atom)